Four-core cables – Why these should be avoided in drive installations?
Many installers prefer using four-core cable, as this is the traditional way for many installations and also because it provides an element of convenience, with the earth lead already included within the cable sheath.
However, when earthing a drive system, two aspects need to be considered – personal protection and EMC. The protective earth exists to provide a low impedance path to ground for any 50 Hz current. Similarly, the functional earth for EMC compliance needs to provide a low impedance path to earth for any high frequency current. With a bit of planning, both objectives can be achieved with the same earthing system.
While the earth lead provided in the four-core cable is adequate for personal protection, the four-core cable is unsuitable for ensuring EMC, as it is not symmetrical.
In a three-core cable, the cores are symmetrically arranged and so are the magnetic fields that surround each conductor. With a four-core cable, the lack of symmetry can cause current to be induced in the earth conductor and propagate through the system.
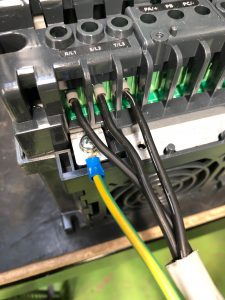
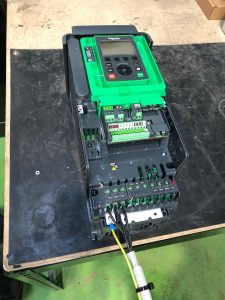
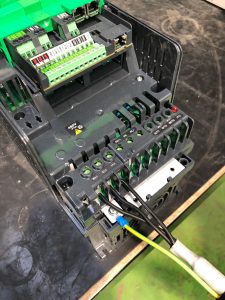
An earthing system to provide both personal and functional earthing should include a three-core supply cable combined with earthing by stranded or braided copper conductors and an external equi-potential bonding cable.
Another earthing practice likely to cause disturbance is when the earth cable is terminated on the earth bar of the drive. While this may seem simple and intuitive, it does not address the need for functional earthing of the enclosure. The earth conductor needs to be terminated at the PE terminal on the VSD metalwork, as well on the PE terminal of the motor. Similarly, the cable braid , or armour, should be terminated at the VSD metalwork. This provides functional earthing and by cross bonding from the VSD metalwork to the enclosure earth bar, safety earthing requirements are met, while ensuring good EMC performance.
A further aspect of good practice is not to use cable above 185 mm2, particularly if the cable is steel armoured. The steel armour has an increased impedance. due to the wire diameter and the skin effect, which causes current to flow near the surface of the conductor. Where larger cross section cable is needed, parallel cables should be used.
If four-core cable must be used for one reason or another, the fourth core needs to be disconnected and insulated at both ends; it should not be used for the earth. Instead, a separate external earth conductor needs to be installed. All of these measures are aimed at providing a lower impedance return path for the high frequency current to the VSD, rather than through the local earth network, possibly via another device that is susceptible to electromagnetic interference.